Moment of truth
Got to the garage at about 1pm on Friday. left at 4.30pm :s
Got the car on the ramps for tracking after fitting the rear beam, ball joints and new suspension. Been driving with the band on the wheel pointing to 10 o'clock, very weird. It is also likely that the tracking was very much out of Alignment.
They had a really good hawkeye alignment system so I took full advantage of that. I asked for maximum caster, -2 camber and 0 toe.
After an hour and a half on the ramp the manager came over as a queue was starting to form.
Unfortunately, we were no where near the targets at this point because the guy doing the setup refused to believe the silver project camber adjusters could also alter camber. This was because they had only seen camber plate top mounts that are bolted to the chassis and set purely for camber adjustment.
Had to get off the ramp for about an hour to get the other 4 cars in the queue through.
(can see the vinyl on the front bumper de laminating, happened on the first sunny day unfortunately and then started to rip with stone chips and rain.)
Then back on the ramps, another mechanic came over, one I have dealt with before, he actually listened to what I was saying and set the top mounts with the slot facing about 45deg from the travel of vehicle direction. The set up plan was max caster by sliding the strut as far back as possible and then rotate the top mount to set the camber. Set the toe and readjusted slightly.
This is what we finished with in the end:
Been for a couple of drives now and the car feels better than it has ever done in the past, really pleased. Corners very hard and grips much better. Next step: Get bumpers sprayed and then Powerrrrrrrrrrr.
Cheers, Ash
Got to the garage at about 1pm on Friday. left at 4.30pm :s
Got the car on the ramps for tracking after fitting the rear beam, ball joints and new suspension. Been driving with the band on the wheel pointing to 10 o'clock, very weird. It is also likely that the tracking was very much out of Alignment.
They had a really good hawkeye alignment system so I took full advantage of that. I asked for maximum caster, -2 camber and 0 toe.
After an hour and a half on the ramp the manager came over as a queue was starting to form.
Unfortunately, we were no where near the targets at this point because the guy doing the setup refused to believe the silver project camber adjusters could also alter camber. This was because they had only seen camber plate top mounts that are bolted to the chassis and set purely for camber adjustment.
Had to get off the ramp for about an hour to get the other 4 cars in the queue through.
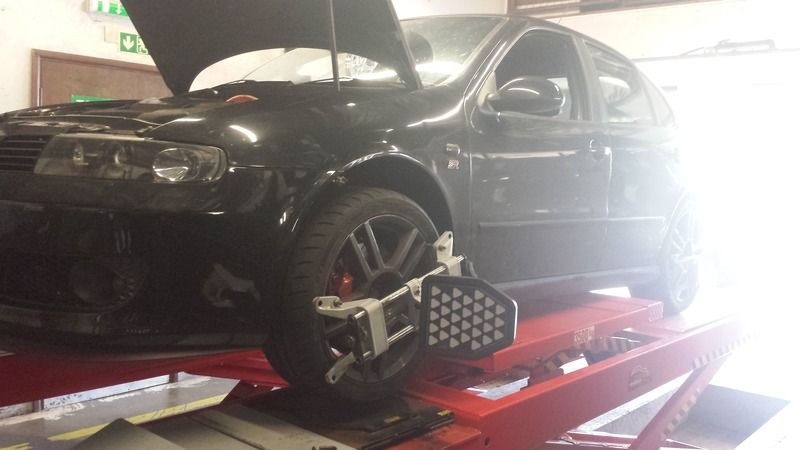
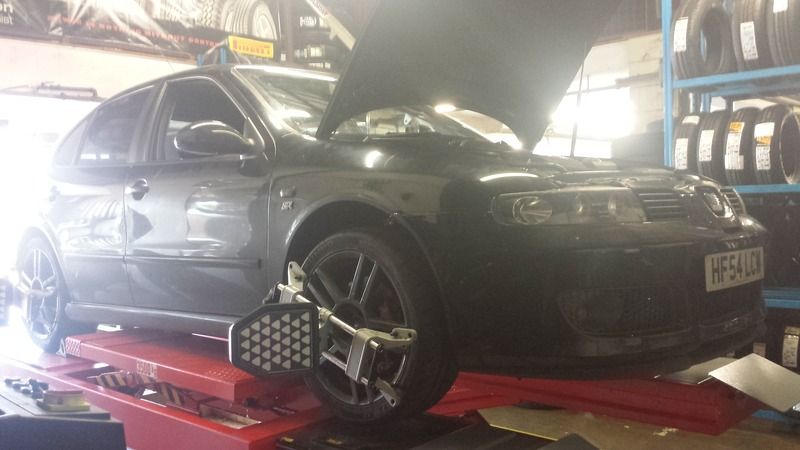
(can see the vinyl on the front bumper de laminating, happened on the first sunny day unfortunately and then started to rip with stone chips and rain.)
Then back on the ramps, another mechanic came over, one I have dealt with before, he actually listened to what I was saying and set the top mounts with the slot facing about 45deg from the travel of vehicle direction. The set up plan was max caster by sliding the strut as far back as possible and then rotate the top mount to set the camber. Set the toe and readjusted slightly.
This is what we finished with in the end:
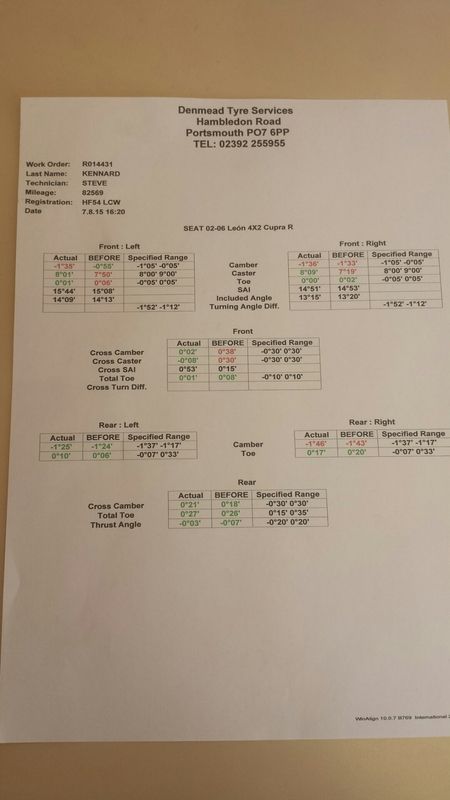
Been for a couple of drives now and the car feels better than it has ever done in the past, really pleased. Corners very hard and grips much better. Next step: Get bumpers sprayed and then Powerrrrrrrrrrr.
Cheers, Ash
Last edited: