I had the chance last week to do some extensive high load testing of the car, and came up with some of the following findings.
Lack of linearity in the power delivery
I was getting a slightly flat/surge power delivery at times depending on what under bonnet temps the car was running at. After extended journeys (where you would expect a good dose of heat soak), I was getting a slightly lazy power delivery, particularly from a mid range acceleration perspective.
Also I was getting an intermittent but very subtle flat spot at around 5000rpm.
Investigations
There are a couple of areas that have always had me scratching my head about the ITG's design
1) The fact that the pipework is metal
2) The fact that the pipework connects directly to a metal mounting point on the block (rather than having a dampened mount like the OEM rubbers on the mounting - WHY: potential vibration to the MAF and hence long term damage, and heat transfer from the block)
3) The heat shield for the filter head whilst good (in theory) restricts the main source of airflow into the engine bay, and hence onto the filter head (noted changes in linearity of power delivery when I changed from the prototype sponge heatshield to the final production unit with a metal plate attached to it)
4) The fact the pipework goes from huge to 67mm right ahead of the MAF causing potential air disruption that may confuse the MAF readings.
Whilst I accept I am NO expert in air filtration, intake systems, and am VERY mindful of the constraints within the bay ITG have had to work around (routing / MAF scaling / mounting points etc..), I'd be very interested to hear the points of views of other owners.
RESOLUTIONS
1) Heat shielding
I went onto the bay to purchase some fairly inexpensive heat wrap (10m roll of 2.5" thick heat tape - self adhesive was £16). This tape has a maximum resistance to heat of 1100 degrees.
I wrapped all the main pipes of the intake system (that were metal), as these were getting incredibly hot after extended runs. Yes there is a heat shield to protect from the worst of the turbos heat output, but come to a standstill for any length of time and the pipes just start to cook. I wasn't sure if this may have any affect on the MAF readings as the air temps inside the pipes must increase when the pipe wall temps increase significantly. I made sure to work around all the main points like the MAF housing, and even taped up the underside of the ITG heat shield plate (nearest the turbo).
After 2 back to back laps of the Ring, I opened the bonnet and put both hands on the pipes of the intake. Whereas before I couldn't have kept my hands on them, they were almost cool to the touch. Yes we hadn't been sat about that long, but we had subsequently queued in traffic to get back to the main car park. I could even hand touch the heat shield plate at the back of the engine which has never been possible after a run before.
Also there is a second benefit for me here. After the HPFP was installed I started to get a noticeable ticking in the cabin whenever the revs went up over 4000rpm. Wrapping the pipework in this tape has suppressed this significantly leading me to believe the HPFP / some part of the fueling system (maybe fuel return valve) naturally ticks, and this was being picked up and accentuated through the ITG's pipework. It's now barely audible at all. The addition of the tape has stopped some of the shrill sucking sound, but actually means we can better hear the exhaust which isn't a bad thing.
2) Pipe connections
The ITG comes with decent jubilee clips, so I'd never really expected any connectivity issues. However when taking the system apart for the first time I noted the pipe going down the back of the bay towards the turbo was incredibly loose (I guess over time with the heat things expand). As I pulled off the pipe which is connected to the metal heat shield plate at the back of the engine, the silicone hose which goes down the back of the engine bay just fell straight off with it leaving me to wonder how tight it was actually connected. Further investigations showed that where the silicone hose connects to the turbo unit, there were oily deposits around the edge of the pipe which as not particularly conducive to the silicone pipe making good contact.
I cleaned all of the connection points with a citrus degreaser, and then all the meal connections with Halfords Surface cleaner to ensure the best possible connections. I then re-fitted all the (dried and cleaned) silicone hoses and got a Laser flexi-shaft 6mm hex head driver to tighten all of the jubilee clips to a fairly decent torque.
When it got to the point of connecting the metal pipe that connects the ITG to the engine block (by the batter), I attached a piece of heat resistant tape to both the ITG mounting bracket and onto the engine block to try and limit any heat transfer between the two components.
It all went back together well, and was about a 1 hour job for a mechanical luddite like myself.
RESULTS:
I'm always very mindful I don't want to be wasting people's time or money on follies like this, as time is precious and money can often be better spent than on half-cocked measures which have little real world benefits.
I have to say, in my personal opinion the car feels quite a bit improved on the road. I inadvertently fixed the idle issue I had by locating a separate pipe leak whilst doing this job, but I don't believe it will affect other changes I have noticed.
1) The flat spot at 5000rpm appears to be gone
We did a good few runs on the de-restricted autobahn, and you don't need a VCDS system to give you a feel for malaise in the car. The car now seems to pull harder, more repetitively and for longer since lagging and re-fitting the pipes. On the track there was definitely more acceleration urgency later in the lap, whereas at Castle Combe in October I was finding the car quite lazy by the end of the stint.
2) The acceleration seems more linear
I don't think this is actually down to the lagging, but it's hard to tell. I actually believe that this is down to the removal of the heat shield by the filter head. Whilst I believe it does serve a purpose, I'm not convinced it's benefits outweigh it's cons. As my S3 was used as a donor vehicle for testing the ITG, initially I had a fully foam based heat shield for the filter head. When the new kits were produced, to increase the heat resistance and the structural rigidity (the foam ones bent after a while), they added the metal glued plate. I purchased one and straight away noted a change in the acceleration characteristics (slightly lumpier). I'm not sure how much forced air the filter head gets from the fog light intake, but again, this air will not be as directive as the air which comes from the grille area. I am currently contemplating looking at intake scoops which will feed air directly to the filter head whilst masking off the engine block.
Please note at this point I am NOT suggesting you go hacking the metal plates off your foam backings (it will rip the foam), but it may be worth running with and without to see whether you notice any difference. Below is a picture of the configuration I am currently running.
3) Air disruption to the MAF from pipework diameter changes
I'm not quite sure how to approach this, but Storm Developments are going to help me install a 67mm pipe that goes back towards the battery from the MAF in due course. Once we have conducted the testing I'll post some results later. It's all guesswork at present, and may deliver no tangible benefits.
DISCLAIMER
Please note, the changes made to my set up were in response to hunting out an issue resolution with an idle. The changes I have made seem to have made a marked improvement to repetitive performance on my car acceleration wise, particularly when running hot. It's not rocket science to suggest heat shielding will deliver a benefit as it's well know heat causes inefficiencies with respect to engine performance. I think in set ups like stage 2+ where boost levels and under bonnet temps may be higher, and you are pushing the car further this pipe lagging may offer more benefit than in more standard set ups.
I can't guarantee it will benefit your car, and to date I have done no data logging to see what the changes equate to. It's all gut feel from being out on the road / track.
If you do this work, ensure you have the right tools and a level of competence as some of the pipes (like the one to the turbo) can be a pain to fit, and don't rely on a magnet to pick up fallen parts as most of them are stainless!!
Always be methodical laying out the parts as you take them off, particularly parts like the spacers and washers for the block connections.
BUT MOST IMPORTANTLY, periodically check the connection of your pipework (annually) to ensure it is tight and well sealed.
I feel given the 1,500 mixed journey miles I've driven in the last week or so I can heartily recommend the heat lagging tape if nothing else (LINK TO PRODUCT).
Any questions, fire away!
Cheers
Warren
Lack of linearity in the power delivery
I was getting a slightly flat/surge power delivery at times depending on what under bonnet temps the car was running at. After extended journeys (where you would expect a good dose of heat soak), I was getting a slightly lazy power delivery, particularly from a mid range acceleration perspective.
Also I was getting an intermittent but very subtle flat spot at around 5000rpm.
Investigations
There are a couple of areas that have always had me scratching my head about the ITG's design
1) The fact that the pipework is metal
2) The fact that the pipework connects directly to a metal mounting point on the block (rather than having a dampened mount like the OEM rubbers on the mounting - WHY: potential vibration to the MAF and hence long term damage, and heat transfer from the block)
3) The heat shield for the filter head whilst good (in theory) restricts the main source of airflow into the engine bay, and hence onto the filter head (noted changes in linearity of power delivery when I changed from the prototype sponge heatshield to the final production unit with a metal plate attached to it)
4) The fact the pipework goes from huge to 67mm right ahead of the MAF causing potential air disruption that may confuse the MAF readings.
Whilst I accept I am NO expert in air filtration, intake systems, and am VERY mindful of the constraints within the bay ITG have had to work around (routing / MAF scaling / mounting points etc..), I'd be very interested to hear the points of views of other owners.
RESOLUTIONS
1) Heat shielding
I went onto the bay to purchase some fairly inexpensive heat wrap (10m roll of 2.5" thick heat tape - self adhesive was £16). This tape has a maximum resistance to heat of 1100 degrees.
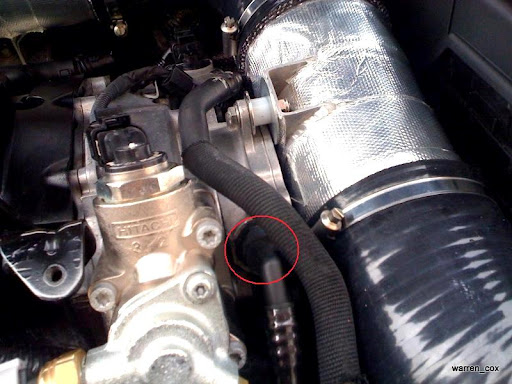
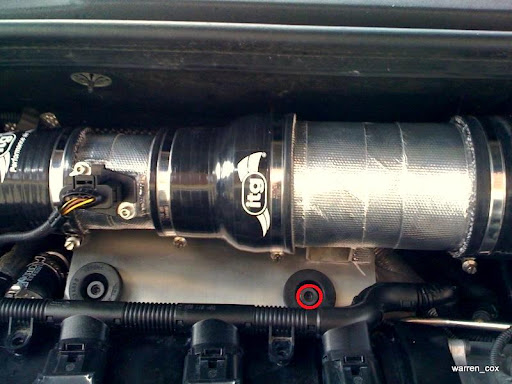
I wrapped all the main pipes of the intake system (that were metal), as these were getting incredibly hot after extended runs. Yes there is a heat shield to protect from the worst of the turbos heat output, but come to a standstill for any length of time and the pipes just start to cook. I wasn't sure if this may have any affect on the MAF readings as the air temps inside the pipes must increase when the pipe wall temps increase significantly. I made sure to work around all the main points like the MAF housing, and even taped up the underside of the ITG heat shield plate (nearest the turbo).
After 2 back to back laps of the Ring, I opened the bonnet and put both hands on the pipes of the intake. Whereas before I couldn't have kept my hands on them, they were almost cool to the touch. Yes we hadn't been sat about that long, but we had subsequently queued in traffic to get back to the main car park. I could even hand touch the heat shield plate at the back of the engine which has never been possible after a run before.
Also there is a second benefit for me here. After the HPFP was installed I started to get a noticeable ticking in the cabin whenever the revs went up over 4000rpm. Wrapping the pipework in this tape has suppressed this significantly leading me to believe the HPFP / some part of the fueling system (maybe fuel return valve) naturally ticks, and this was being picked up and accentuated through the ITG's pipework. It's now barely audible at all. The addition of the tape has stopped some of the shrill sucking sound, but actually means we can better hear the exhaust which isn't a bad thing.
2) Pipe connections
The ITG comes with decent jubilee clips, so I'd never really expected any connectivity issues. However when taking the system apart for the first time I noted the pipe going down the back of the bay towards the turbo was incredibly loose (I guess over time with the heat things expand). As I pulled off the pipe which is connected to the metal heat shield plate at the back of the engine, the silicone hose which goes down the back of the engine bay just fell straight off with it leaving me to wonder how tight it was actually connected. Further investigations showed that where the silicone hose connects to the turbo unit, there were oily deposits around the edge of the pipe which as not particularly conducive to the silicone pipe making good contact.
I cleaned all of the connection points with a citrus degreaser, and then all the meal connections with Halfords Surface cleaner to ensure the best possible connections. I then re-fitted all the (dried and cleaned) silicone hoses and got a Laser flexi-shaft 6mm hex head driver to tighten all of the jubilee clips to a fairly decent torque.
When it got to the point of connecting the metal pipe that connects the ITG to the engine block (by the batter), I attached a piece of heat resistant tape to both the ITG mounting bracket and onto the engine block to try and limit any heat transfer between the two components.
It all went back together well, and was about a 1 hour job for a mechanical luddite like myself.
RESULTS:
I'm always very mindful I don't want to be wasting people's time or money on follies like this, as time is precious and money can often be better spent than on half-cocked measures which have little real world benefits.
I have to say, in my personal opinion the car feels quite a bit improved on the road. I inadvertently fixed the idle issue I had by locating a separate pipe leak whilst doing this job, but I don't believe it will affect other changes I have noticed.
1) The flat spot at 5000rpm appears to be gone
We did a good few runs on the de-restricted autobahn, and you don't need a VCDS system to give you a feel for malaise in the car. The car now seems to pull harder, more repetitively and for longer since lagging and re-fitting the pipes. On the track there was definitely more acceleration urgency later in the lap, whereas at Castle Combe in October I was finding the car quite lazy by the end of the stint.
2) The acceleration seems more linear
I don't think this is actually down to the lagging, but it's hard to tell. I actually believe that this is down to the removal of the heat shield by the filter head. Whilst I believe it does serve a purpose, I'm not convinced it's benefits outweigh it's cons. As my S3 was used as a donor vehicle for testing the ITG, initially I had a fully foam based heat shield for the filter head. When the new kits were produced, to increase the heat resistance and the structural rigidity (the foam ones bent after a while), they added the metal glued plate. I purchased one and straight away noted a change in the acceleration characteristics (slightly lumpier). I'm not sure how much forced air the filter head gets from the fog light intake, but again, this air will not be as directive as the air which comes from the grille area. I am currently contemplating looking at intake scoops which will feed air directly to the filter head whilst masking off the engine block.
Please note at this point I am NOT suggesting you go hacking the metal plates off your foam backings (it will rip the foam), but it may be worth running with and without to see whether you notice any difference. Below is a picture of the configuration I am currently running.
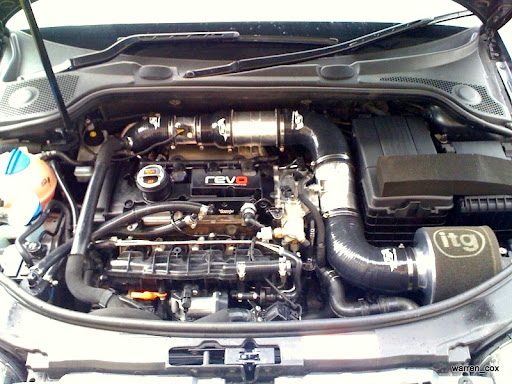
3) Air disruption to the MAF from pipework diameter changes
I'm not quite sure how to approach this, but Storm Developments are going to help me install a 67mm pipe that goes back towards the battery from the MAF in due course. Once we have conducted the testing I'll post some results later. It's all guesswork at present, and may deliver no tangible benefits.
DISCLAIMER
Please note, the changes made to my set up were in response to hunting out an issue resolution with an idle. The changes I have made seem to have made a marked improvement to repetitive performance on my car acceleration wise, particularly when running hot. It's not rocket science to suggest heat shielding will deliver a benefit as it's well know heat causes inefficiencies with respect to engine performance. I think in set ups like stage 2+ where boost levels and under bonnet temps may be higher, and you are pushing the car further this pipe lagging may offer more benefit than in more standard set ups.
I can't guarantee it will benefit your car, and to date I have done no data logging to see what the changes equate to. It's all gut feel from being out on the road / track.
If you do this work, ensure you have the right tools and a level of competence as some of the pipes (like the one to the turbo) can be a pain to fit, and don't rely on a magnet to pick up fallen parts as most of them are stainless!!
Always be methodical laying out the parts as you take them off, particularly parts like the spacers and washers for the block connections.
BUT MOST IMPORTANTLY, periodically check the connection of your pipework (annually) to ensure it is tight and well sealed.
I feel given the 1,500 mixed journey miles I've driven in the last week or so I can heartily recommend the heat lagging tape if nothing else (LINK TO PRODUCT).
Any questions, fire away!
Cheers
Warren
Last edited: